Onshore wind turbine Schaefer A35 gearbox refurbishment
Onshore wind turbine Schaefer A35 gearbox refurbishment
Jahnel Kestermann (JAKE) / Schaefer
Project details
Brief: | Main gearbox refurbishment – replacement parts and repair where possible |
Application: | Onshore wind farm – Endurance wind turbine |
Gearbox Original Equipment Manufacturer: | Jahnel Kestermann (JAKE) / SchaeferHelical, mono-block, 3 Stage, 68.8: 1 unit for 500kW wind turbine |
Reported Problem: | Catastrophic failure in service |
Results: | Refurbishment completed with rapid turnaround. New bearings and consumables. Gear case recovered. Parts salvaged where possible, replacement components where not, saving on downtime and on cost to client. This is Dana SAC UK’s fourth refurbishment on this type of unit. |
As received
The main gearbox had failed catastrophically, in service. This gearbox problem has affected a number of this type of turbine.
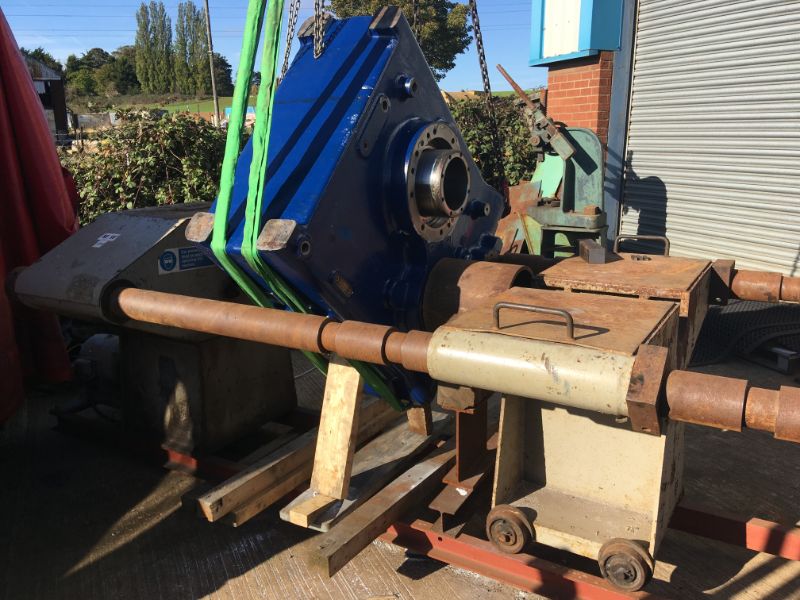
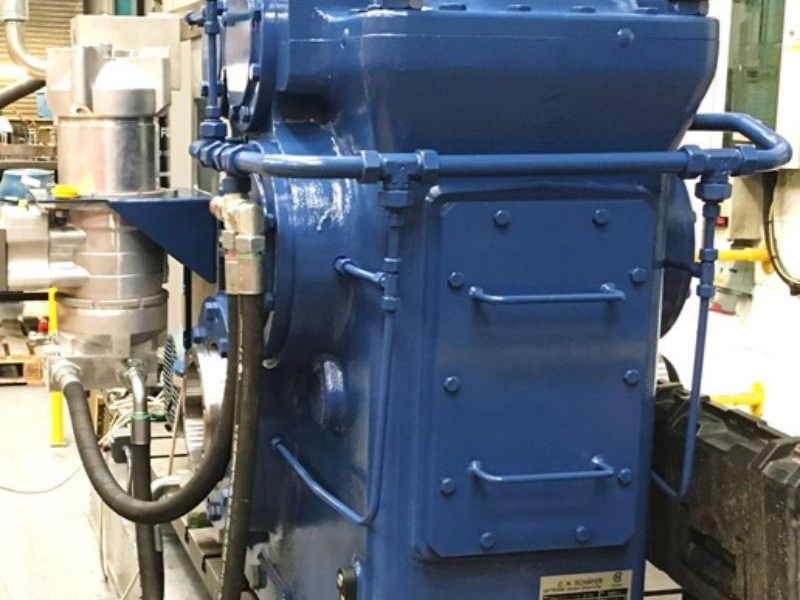
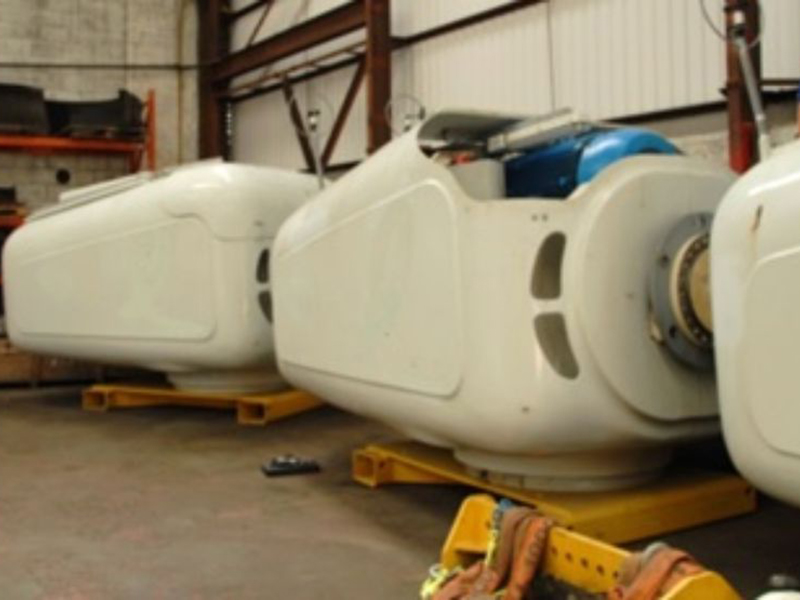
Strip down and investigation
Examples at varying stages of failure, enabling identification of the point of initiation.
Bearings on the second line being overloaded causing bearing failure. Subject to how long the unit continues to run, the case bores and second and third line gearings destroyed.
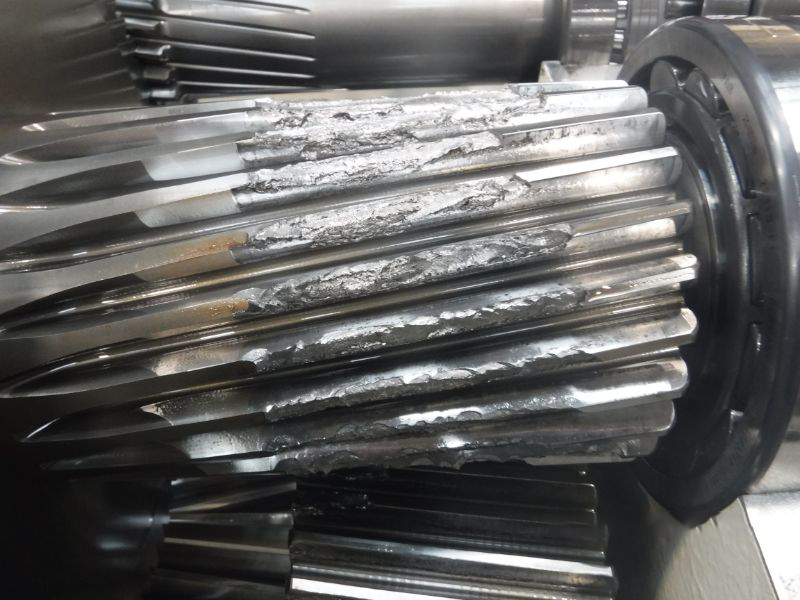
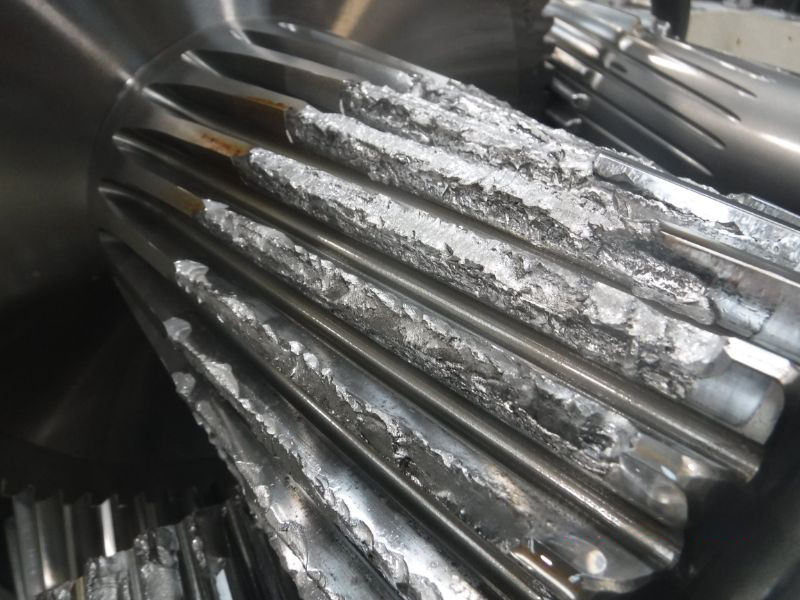
Further analysis
Prime contributor to failure found to be thrust overload, seen from asymmetrical bearing inner race wear.
Low speed shaft interface also damaged at original installation.
Though high value components had been written off, detailed analysis and non-destructive testing showed refurbishment to be commercially viable.
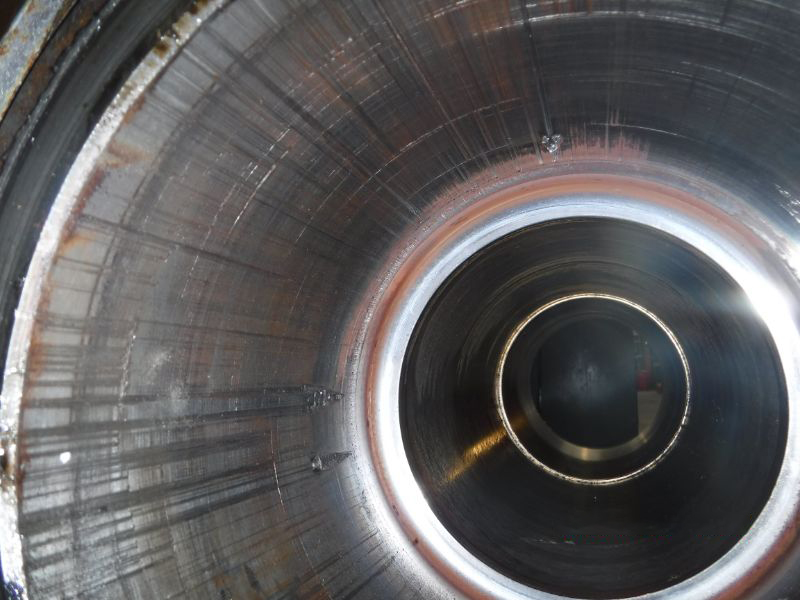
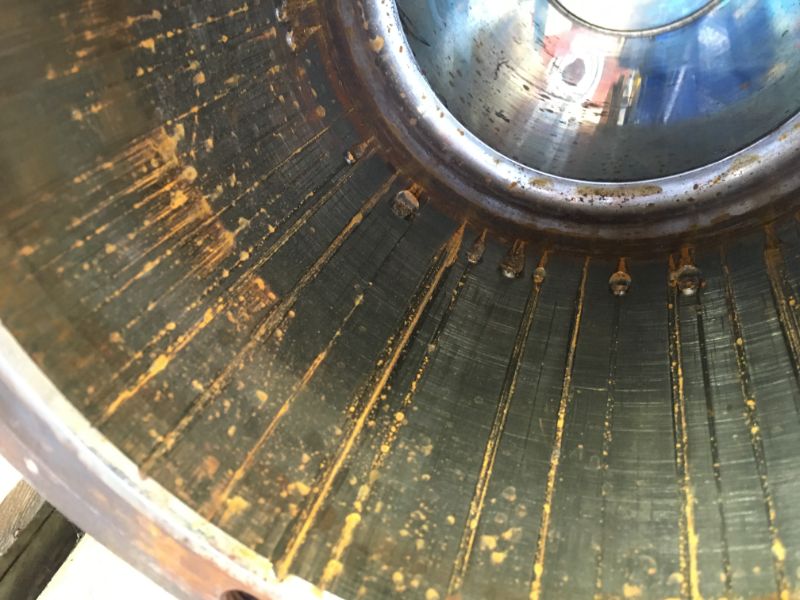
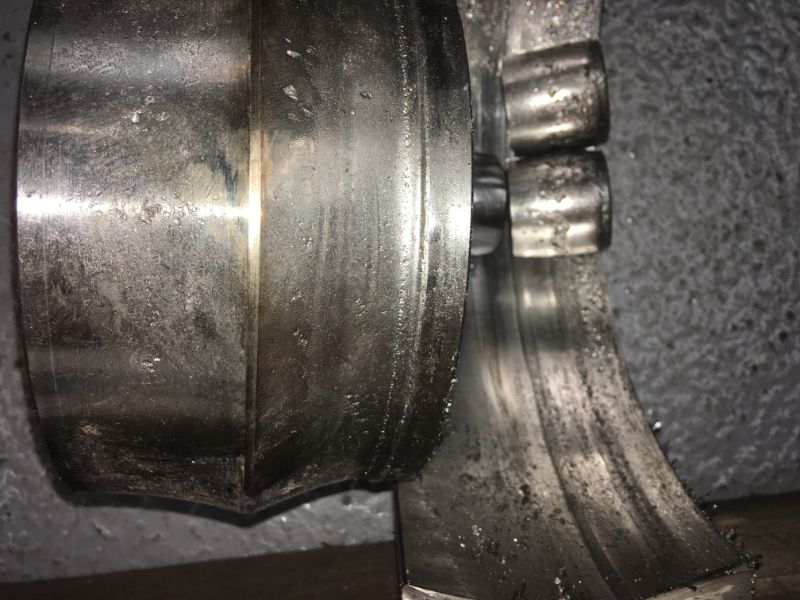
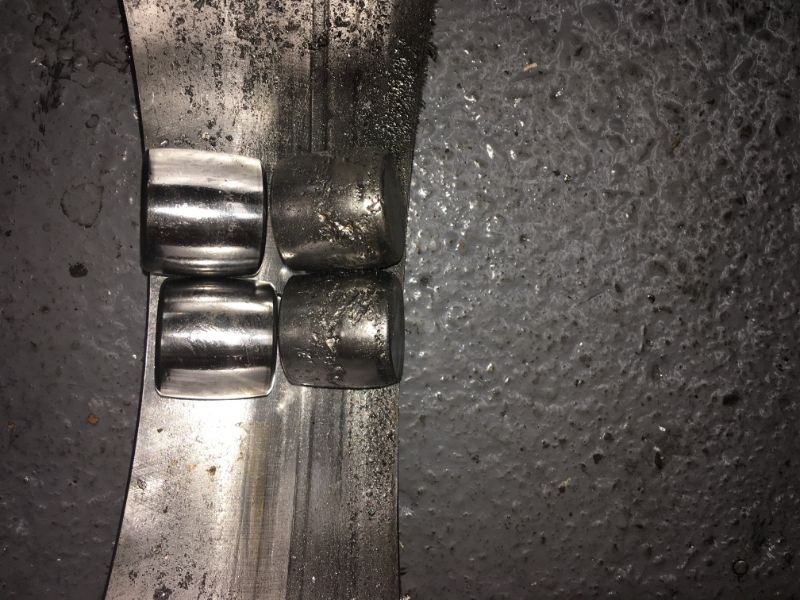
Reporting and recovery options
In-depth investigation informed a detailed report with fully-costed recommendations.
Damage rendering parts unusable illustrated and explained.
Reusable parts and replacement parts clearly identified, allowing accurate rebuild cost to be quoted. Optional elements made clear.
Gearcase recovery with top hat liners
Gearcase set up and clocked on the horizontal borer to complete pre-quote investigation.
This confirmed that general accuracy of the gearcase is good – parts of both the bore pair were unworn.
The line then re-bored oversize with a counter bore added for the Top Hat flange.
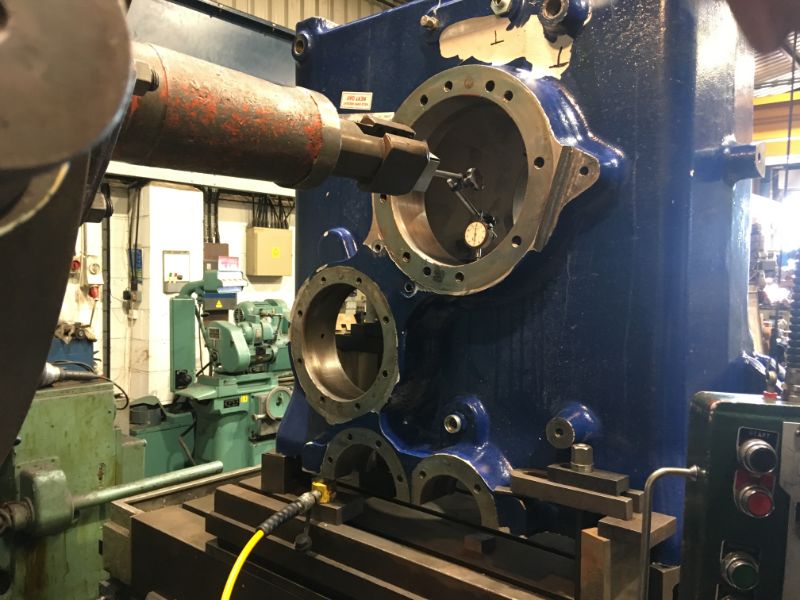
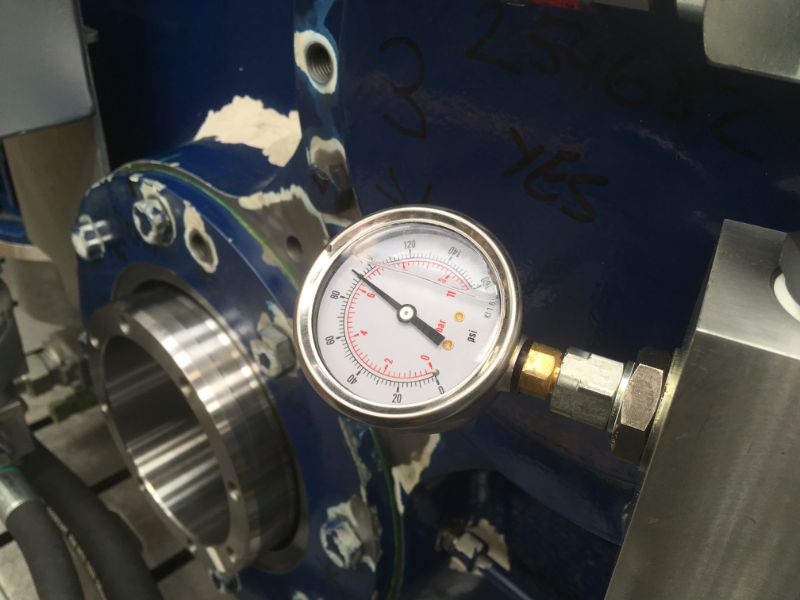
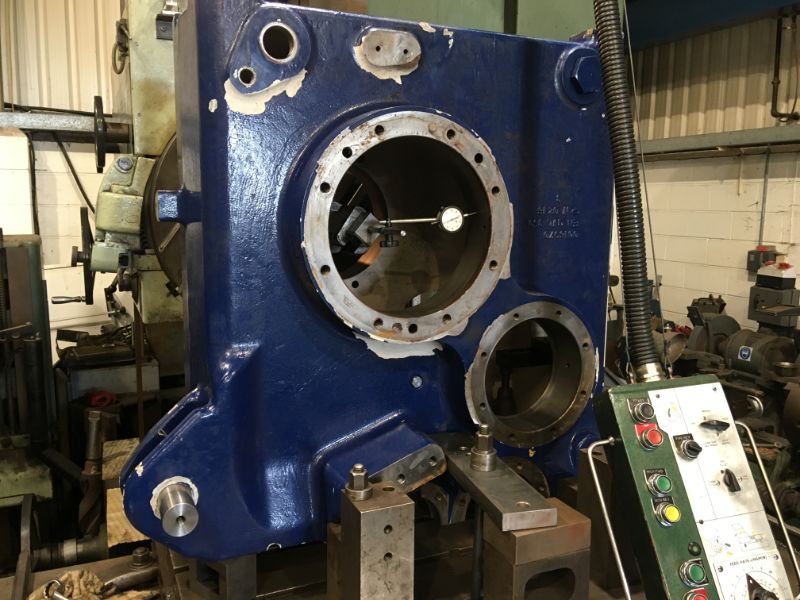
Build with existing and new parts
The unit has helical gearing throughout.
Partly mono-block in design, making strip down and gear wheel installation challenging.
Bore liners fitted prior to installing bearings.
Axial floats set, checked and recorded.
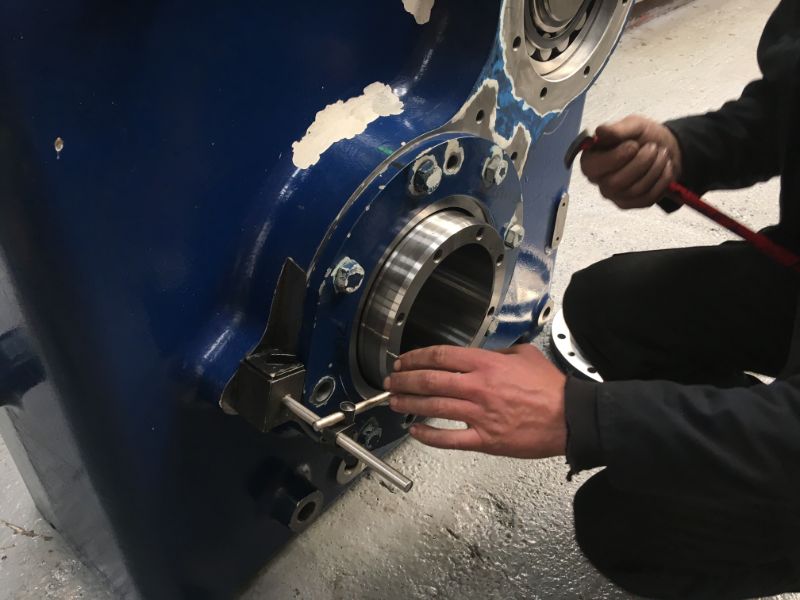
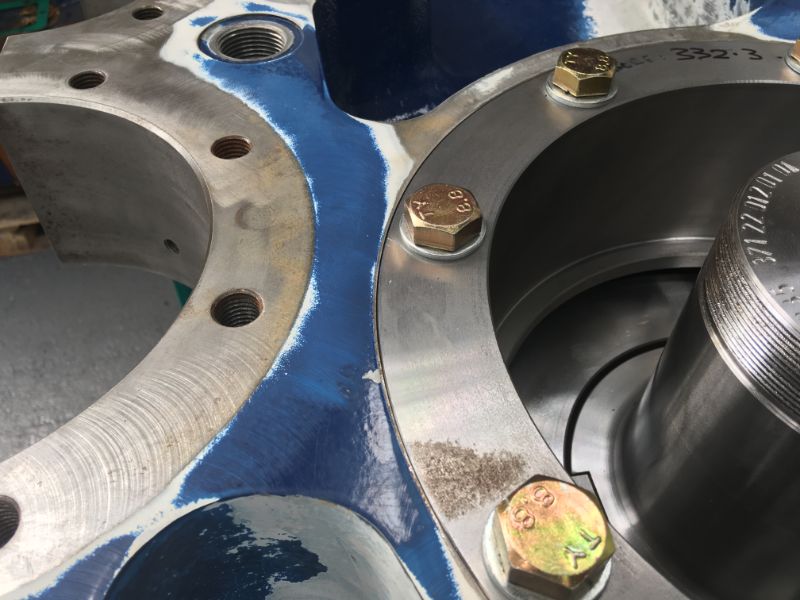
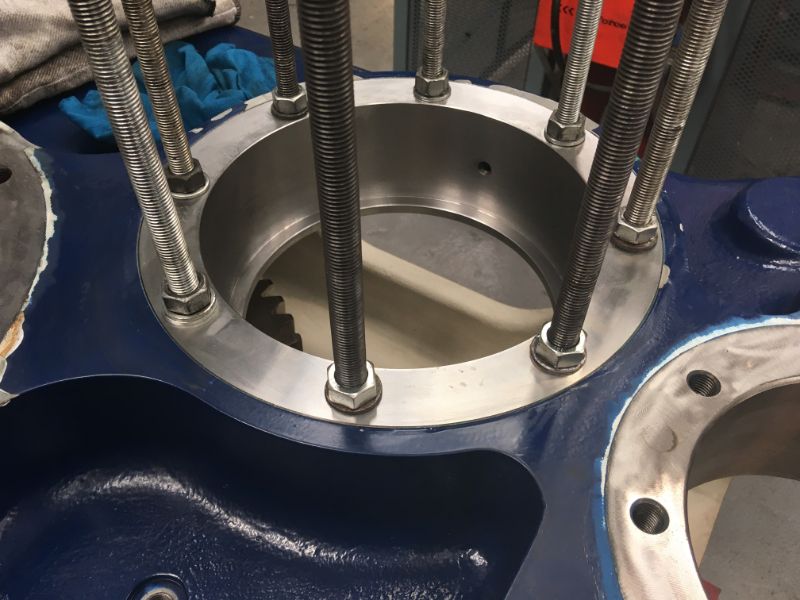
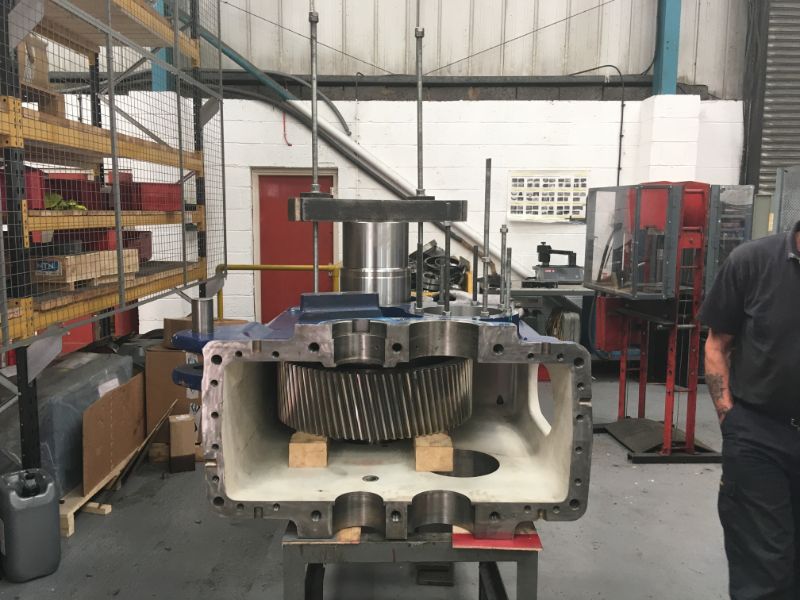
Test, paint and despatch
Internals reset and gear contacts verified.
Unit is spin tested with bearing temperatures monitored to ensure they plateau at an acceptable level.
Lube system checked. Run with a test filter element, replaced with new on completion. Upgraded third party system fitted.
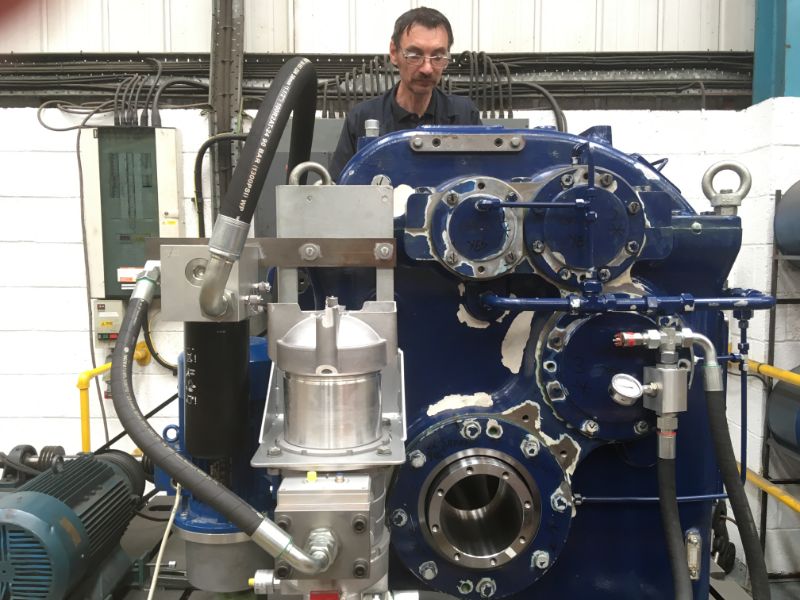
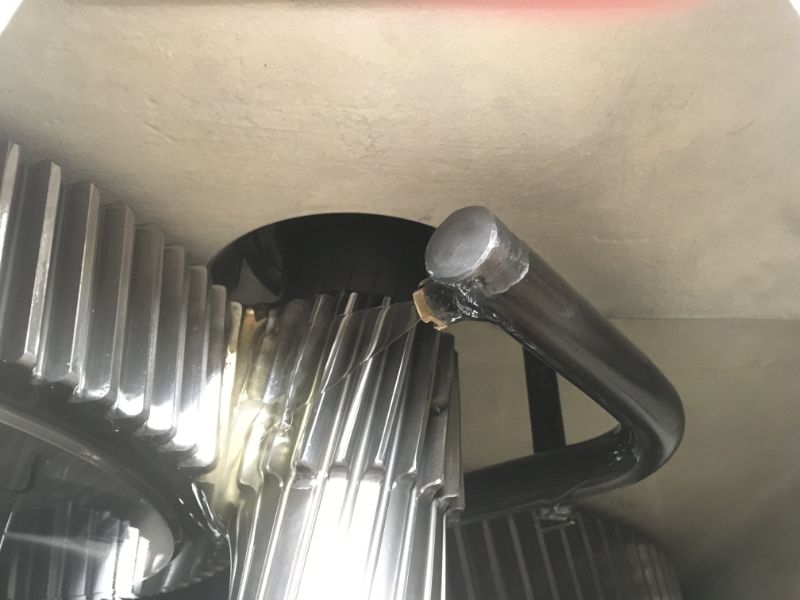
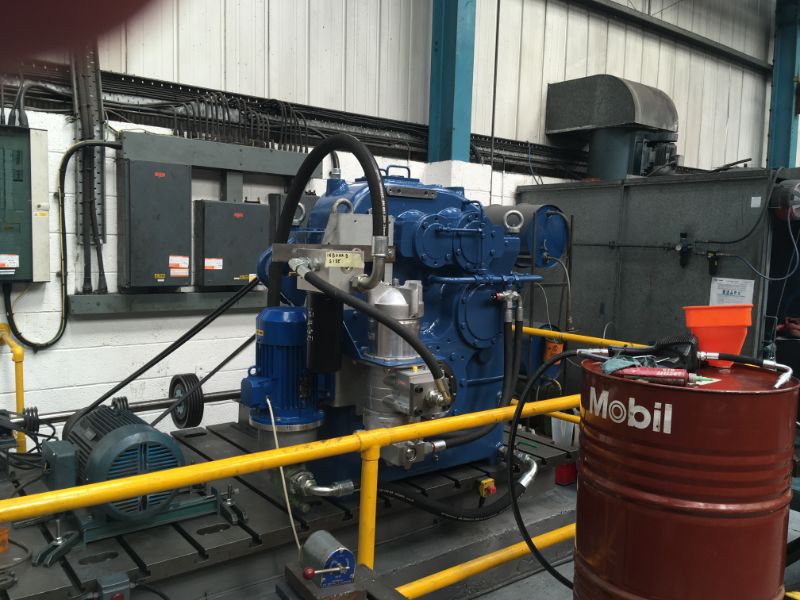
Results
Refurbishment possible, even for most extensive damage, at less than half the cost of a new unit.
Choice between OEM gear parts or reverse-engineered items from UK independent gear cutter at reduced cost and substantially reduced lead time.
All reused parts subject to NDT (magnetic particle inspection).
All new parts and workmanship with 12-month warranty.
Summary
This is the fourth such refurbishment project undertaken by our Servicing team, with a fifth one underway. Experienced with main gearboxes from numerous manufacturers, up to / including V52 size, with many of this type of gearbox serviced and value added to some of the most badly damaged units. Dana SAC UK gearbox technicians and engineers available for up turbine work in the field – including borescope VA inspections and HSS bearings replacements.