Minimising outages for onshore renewables – gearbox inspection and maintenance for profitable power production
2017 is, arguably, a pivotal year in O&M strategy for the UK wind power industry, with many long-term service contracts reaching the end of their term. Here, Andrew Baggaley, Aftermarket Manager at Dana Brevini UK, considers the elements of gearbox inspection for onshore renewables.
Inspection of sun pinion wear marks
Well-established in the UK, the wind farm sector is now facing a raft of uncertainties, not least the impact of Brexit and relations with the EU – a significant proponent of renewable energy. That said, investment in the UK continues to be strong and the Wind Europe report, ‘Wind in Power, 2016 statistics’, published this month, indicates that the UK was, again, the largest EU investor in wind power, at 46% of total European financing. These trends, combined with the general challenges faced by O&M managers, mean that the consideration of gearboxes – as an integral part of the wind turbine – has never been more pertinent.
Gearbox inspection is crucial and, with over 10 years’ experience in the renewable energy sector, servicing wind farms throughout Britain, Brevini UK are ideally-placed to discuss the benefits of planned preventative maintenance (PPM) as well as general inspection, repair and refurbishment for onshore wind power providers.
A 2014 report from GCube found that there are around 1,200 incidents of gearbox failure reported each year, one per 145 turbines in operation. With O&M costs representing about a quarter of total-life costs for wind power plants, keeping gearboxes maintained and working is crucial to the successful and profitable running of any wind power project. Similarly, WEU’s 2015 report suggests that, while many components are repaired quickly, gearbox failures can cause the longest outages, at 5.4 days. The WEU report indicates that one reason for the relatively long outages caused by gearbox failure is the long lead time in sourcing or securing spare parts.
Typical image of surface damage to a roller bearing element
When considering a contractor for inspection and servicing for gearboxes, commercial purchasing power can be a key factor. As Andrew comments,
“Brevini have vast experience of refurbishing all models and makes of gearboxes and, as a gearbox manufacturer ourselves, we can draw on resources across our UK and international supply chain. In the case of wind turbines, we inspect large numbers of units annually. This incorporates a wide range of manufacturers’ main gearboxes across a range of configurations up to and including the 60M Rotor Diameter size and we refurbish both main gearboxes and yaw drives. Our expertise helps us work with our clients to reduce the impact of any repair, refurbishment or replacement found necessary as part of a PPM schedule or due to failure outside of our routine inspection cycle, saving valuable time for our clients – days that could otherwise be lost for power-generation.”
Diagnostic techniques have changed quite dramatically over recent years. In part, this can be attributed to the rapid growth of the sector and the increasing demand for high energy-generating capacity, with a trend towards larger gearboxes. All this comes with new maintenance issues and considerations and, in this respect, Brevini UK enable wind farm operators and O&M providers to take a proactive approach through rigorous inspection and analysis, providing detailed reports as part of their service offering.
An inspection for wind turbine gearboxes includes: vibration analysis (VA); visual inspection; high resolution still and video images from a state of the art borescope, and oil sampling. The VA can also highlight mechanical issues in the generator itself. Andrew explains this part of the inspection process,
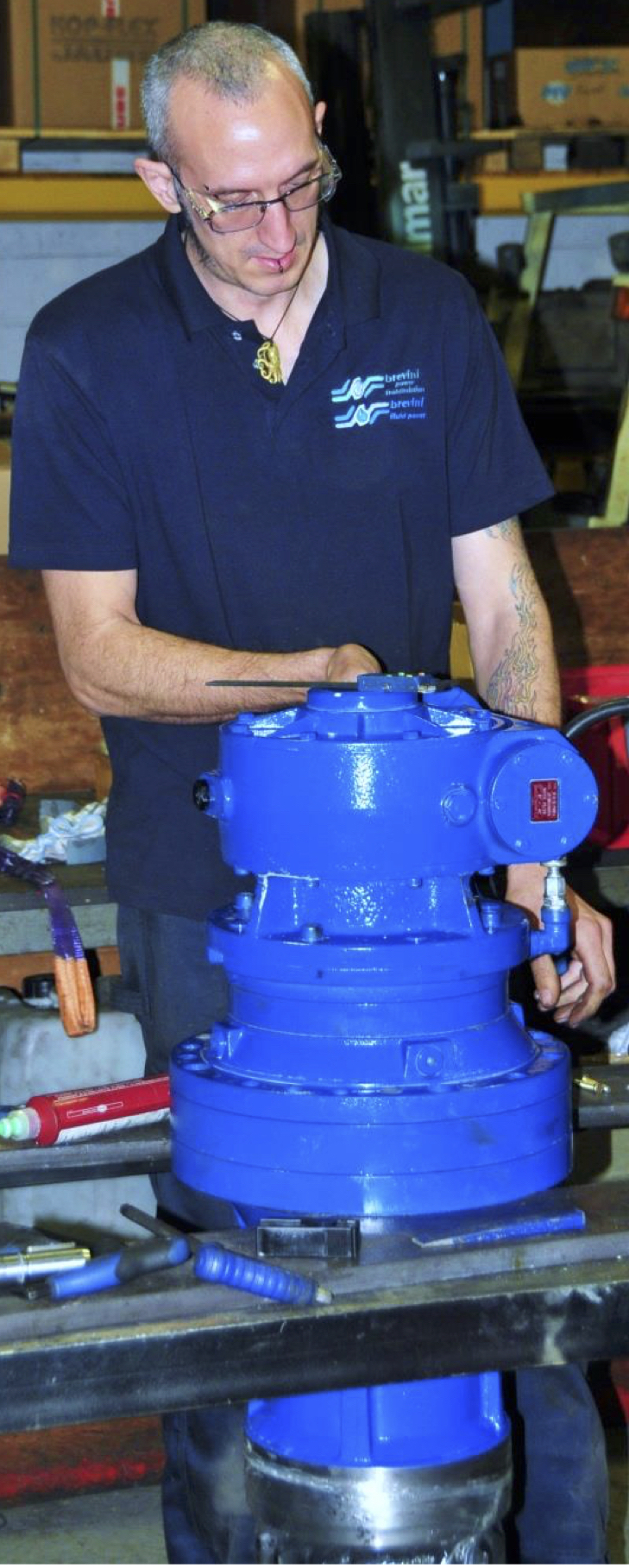
Testing seal integrity on a yaw drive
Additional processing techniques such as synchronous time waveform analysis, real-time recordings and dual channel bode plots allow us to accurately determine the condition of the low speed section of the gearbox such as the planet wheel gears, bearings and sun-wheel pinion. In some cases, these are not easily accessible using remote visual inspection methods alone. An added benefit of using this technology is that inadvertent transmitted vibration from generators with worn bearings, cracked or loose rotor bars or stator wear can also be detected on the high speed section of the gearbox by using vibration analysis.”
Clearly, this type of knowledge is of great benefit, not only to the endoscope inspection engineer who is about to undertake the remote visual inspection, but also to the client, who has a detailed and thorough assessment of the installation, making judgement calls on whether to restrict the speed or isolate the machine – a relatively straightforward task.
A typical Brevini wind turbine main gearbox inspection sees the initial vibration readings lead the borescopic examination. This is important because it is often necessary to persist in finding the visual evidence to confirm the VA result which is often the early warning. It follows that the exercise is not simply the collection of data, but the interpretation – before the opportunity to take a closer look is lost. As Andrew says,
“The expertise on the spot is crucial. The extent to which VA will pinpoint problems can be very impressive. Clients however, generally feel more comfortable taking decisive action when they can see correlation between the VA and the images of the actual surface condition of the bearings and gear faces.”
In addition to the VA and visual evidence, the oil analysis is also a sophisticated tool. Specific metals and contaminants can be linked to specific components e.g. gear parts have specific alloying elements, which are different to bearings or the gear case. All the evidence builds up a picture. When this detail is added to the inspection data it can either be the final confirmation that action is needed or perhaps identify specific factors to be carefully monitored. Anecdotal information often coming from the O&M contractor will also qualify the findings so this relationship is also important. This holistic knowledge allows time to offer cost-effective planned repairs before unnecessary collateral damage occurs.
Clearly, there are technological advances in diagnostic tools available to companies involved in O&M servicing for renewables, all aimed at reducing down-time and avoiding catastrophic failure of gearboxes with the operational and financial impact, that entails. While this is positive, it’s also important to know how to work with such data. As Andrew says,
“The client generally wants to know what level of risk they are exposed to and the options for managing it. The data needs to be accurately interpreted to allow the operator to decide when to act because their costs of intervention are significant. The costs of terminal failure are of course a great deal higher. In many cases the outcome of an inspection is to monitor trends. The real payback, however, is realised when the presence of a critical failure mode is spotted and the underlying cause accurately identified. While inspection and repair activities are often kept independent, the refurbishment of assets is an area where Brevini’s Aftermarket experience and resources can really add value.
It’s important to know that the company you chose to manage your maintenance and servicing are experienced in diagnostic issues and that they have the expertise to establish the difference between normal wear and the advanced stages of a critical failure mode. It is important to respond to each scenario appropriately, to help maximise both the lifespan and the efficiency of such business-critical assets.”